Access Management Expert FDI relies on Ersa Technology User Report
Being on the market since 1989, FDI designs and manufactures access management systems and provides full project support from the concept stage through to production. As a leading manufacturer of access control and intercom systems for buildings, the French company offers a range of products based on the latest technologies and can rely on a highly qualified, interdisciplinary team. In the recent past, FDI has added three Ersa HOTFLOW reflow soldering systems to its electronics production machinery.
One of FDI´s secrets of success is its extensive expertise in product development and design. 46 percent of its current 170 employees work in this sector. Located in Cholet, Maine-et-Loire, the company has been a wholly owned subsidiary of Urmet France, which belongs to the Urmet Italia Group, since 2000 and exports its products to more than 35 countries worldwide.
The expansion of its market activities and the strengthening of its position as a provider of complete solutions from A to Z is based on FDI´s access control/intercom business and the IoT business since the acquisition of the Toulon-based company YOKIS in 2014. In addition to marketing and selling end products under its own brands URMET and YOKIS, the French company develops and manufactures OEM products for the Urmet subsidiaries Castel, MWS and Synchronic.
First contact at GLOBAL INDUSTRIE in Paris
The first contacts between FDI and Kurtz Ersa France were made in 2015 at the GLOBAL INDUSTRIE exhibition in Paris between Jean Gautier, Directeur Industriel of FDI, and Rémy Lutz, Managing Director of Kurtz Ersa France. At the time, FDI was working with a wave soldering system in their THT line, but since the acquisition of YOKIS, it was becoming more and more difficult to meet the increased soldering quality requirements. In its search for alternatives, FDI increasingly turned to the selective soldering technology, and the route to Ersa, the leading manufacturer in this field, was not far. In the past as well as today, reliability, reproducibility, soldering quality, and productivity are the most important factors for the access control experts. The initial contact in Paris was followed by a visit to Ersa in Wertheim, Germany, to thoroughly test the range of selective soldering machines at the Ersa Application Center. This is how the relationship between the two companies began - after intensive consultation, a VERSAFLOW 3/45 selective soldering machine was purchased in 2016, featuring two soldering modules with one solder pot per module as well as top- and bottom-side heating.
The first selective soldering machine was followed by another VERSAFLOW 3/45 in 2017, also equipped with two soldering modules and one solder pot per module. However, this selective soldering system only had a bottom-side heating, since the electronic assemblies to be processed on it are equipped with sensitive wires on its top side, which must not be exposed to unnecessary thermal stress. The wave soldering system from 2014 is still operating today, being used to solder single sided assemblies. Currently, the two selective soldering systems plus three reflow ovens run in a two-shift system from Monday to Friday.
Decision for Ersa Reflow according to benchmark
In 2021 FDI carried out a benchmark to modernize the SMD lines which the Ersa HOTFLOW technology was able to win. Today, the FDI production halls host three HOTFLOW ovens, which enable reflow soldering with excellent thermal performance. The innovative heating technology ensures stable temperature profiles within the machine, and the different process zones can be individually controlled. This guarantees an optimal soldering process while minimizing thermal stress on the components. The integrated heat recuperation and intelligent process control significantly reduce energy and nitrogen consumption. Since all Ersa HOTFLOW systems are easy to maintain, downtimes are also kept to an absolute minimum.
For FDI, purchasing reflow ovens and selective soldering systems from a single supplier also has the advantage that there is a central point of contact for service & maintenance, FDI employees are trained on similar systems and have to deal with comparable human-machine interfaces. To date, FDI has never had to call the Ersa hotline in Germany. “The machine installations and trainings have always gone well, with Ersa´s technical department listening very carefully and giving clear explanations during the training sessions. When it comes to repairs and annual maintenance as part of the maintenance contract, we can rely on the quick response of Ersa´s service department,” says François Lebon, FDI production manager.
Further expansion of market activities planned
In the future, the company plans to further expand its own product lines, which are currently being designed in the FDI design office, as well as to further develop customer-specific OEM products. The next investment phase for continuous quality improvement in the process chain will be the investment in an AOI machine, scheduled to be installed and put into operation in 2025. At the same time, FDI is discussing with its assembly partner the installation and use of “MYCenter Analysis” software to reduce scrap, optimize performance and increase capacity in real time. FDI is also in touch with Ersa so that the “Kurtz Ersa GATE” gateway can exchange process data via the IPC/CFX protocol. Finally, the “Kurtz Ersa CONNECT” services will be implemented to enable further advances in FDI´s production.
Categories
Author
Rémy Lutz
Managing Director Kurtz Ersa France
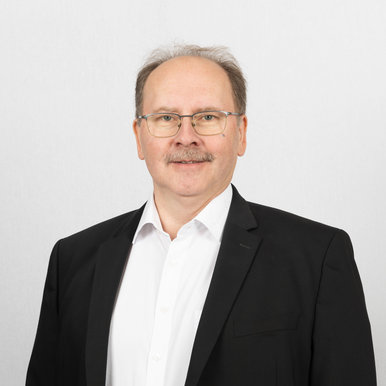