PressFinish uses Ersa Technology
PressFinish Electronics GmbH has been a passionate EMS service provider since the company was founded in 1982. Since April 2024, the company has been manufacturing electronics for its customers in the medical technology, industrial and aerospace sectors at its new 2000 m² site in Maisach near Munich. Selective soldering and paste printing technology from Ersa are also used here.
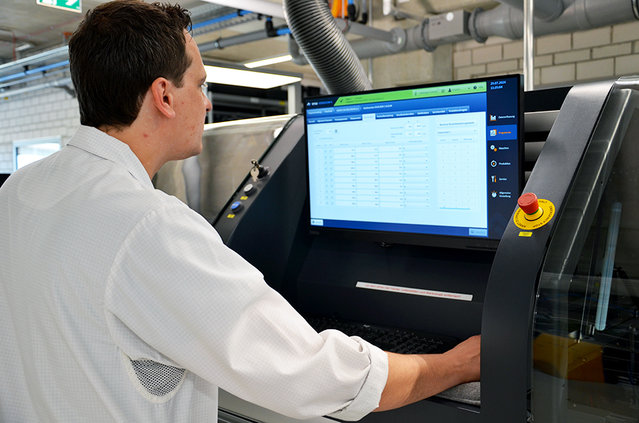
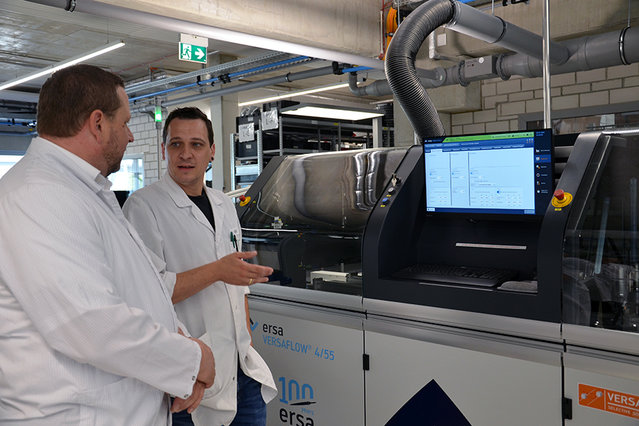
Germany currently has a tough time competing globally. Too cumbersome, too high costs, too much bureaucracy are just some of the issues. So how can companies overcome the challenges posed by the location? For PressFinish, the answer is flexibility, expertise and top quality, which is achieved with a well-trained workforce and modern equipment. “We work to make our customers happy,” is how Production Manager Dominik Wimmer succinctly sums it up when asked about the company spirit.
PressFinish´s range of services reflects this: in production, batch sizes from 1 piece, prototype production through to series with quantities of 100,000 are commonplace. In addition to contract manufacturing, which forms the basis of the company, the development and prototype business has recently grown increasingly. Here, PressFinish offers a complete package if required and develops products from scratch – starting with PCB design and assembly through to the associated housings and software and subsequent prototype production. If a product then enters series production, PressFinish takes over not only production but also component procurement, including warehousing, right through to final assembly and order picking into the customer´s own sales packaging. Customers benefit from a strong team, short distances and direct communication between the individual departments.
The Upper Bavarians have acquired particular expertise in the aerospace (avionics), industrial electronics and medical technology sectors. For example, they manufacture control units for drones and telemetry systems, including functional testing in accordance with IPC-A-600 and IPC-A-610 guidelines. The highlight in the industrial electronics sector is the development and production of explosion-proof electronic assemblies, as PressFinish is ATEX-certified.
The challenge of aluminum laminated boards
However, the largest share of production goes to the medical sector. PressFinish has been active in this sector for over 20 years, developing and manufacturing assemblies and devices for blood testing and processing as well as lighting technology for operating rooms or examination devices that use LEDs as light sources for numerous large and medium-sized companies. These assemblies are generally based on aluminum-laminated printed circuit boards. This is because the heat generated at the LED connections during operation is dissipated via the aluminum layer of these PCBs. When soldering the LEDs, the challenge is therefore to get enough heat to the solder joints in order to achieve a secure, form-fit connection. The processing of such PCBs is one of the areas in which PressFinish specializes.
To apply the solder deposit to the PCBs, PressFinish uses a VERSAPRINT solder paste printer from Ersa, which is equipped with a line scan camera for automatic post-print inspection in the line cycle. As in the automotive industry, complete traceability of the individual production steps is also required in medical technology, avionics and industrial electronics. PressFinish can guarantee this – not a matter of course with a company of 35 employees. “Throughout the company, we know exactly which components from which roll from which batch were used and can provide the associated production data and AOI results,” says sales employee Franz Leitenstern proudly. The relocation to the new company site in Maisach has also enabled the process to be further optimized.
Electronics production changed with the development of SMD technology. THT components were replaced by surface-mounted chips and BGAs, and the trend towards miniaturization really took off. Nevertheless, THT components are still indispensable in the world of electronics. “When high currents have to be absorbed or for connections that require a little more support on the circuit board, through-hole mounting is the first choice,” says sales employee Franz Leitenstern. “We are also getting more projects in power electronics, mobile communications and e-mobility. With these heavy boards with their thick copper layers, you cannot do it without connectors. We don´t process pure SMD assemblies, but always have mixed assemblies with a single-digit percentage of THT.”
To further professionalize THT processing in the company, PressFinish invested in a VERSAFLOW 4/55 selective soldering system from Ersa in 2022. The system impressed with its outstanding soldering quality, its simple operating concept and its inline capability, as the system is automatically fed with the assemblies to be soldered via magazines. Frequent product changes and a wide range of component variants are everyday business at PressFinish. Short set-up times and fast programming of the VERSAFLOW 4/55 provide the necessary flexibility in production. “When we have set up a machine for a production process, we expect it to run after 2 to 3 corrections in the fine adjustment. And we can achieve this with Ersa, because the system is very easy to understand,” explains Dominik Wimmer. PCB panels that are soldered in parallel with the same nozzle diameter are rather rare at PressFinish. A VERSAFLEX soldering module was therefore chosen. The soldering pots are mounted on two independent axes and can be moved individually. PressFinish generally equips the pots with different nozzle diameters in order to solder high-mass connections and delicate solder joints on a PCB simultaneously. To ensure complete traceability for PressFinish customers here too, the VERSAFLOW 4/55 can record the individual process parameters for each individual solder joint of a product in detail and store them in the MES system. This means that they are still available months later if required.
Strong partnership, high level of expertise
If you look at the current trends in electronics at PressFinish, our colleagues are seeing a steadily growing proportion of miniature components on the assemblies and are therefore consistently expanding their expertise in this area. The company regularly pushes the limits of what is physically possible. Everything has to fit, not only the parameters of the production systems, but above all the PCB design. This is where partners with strong expertise are needed. “The strong service that Ersa offers its customers, not only in terms of its products but also in terms of process consulting, was a key reason for the collaboration,” explains Production Manager Dominik Wimmer. “But even with the best preparation and zero-defect strategies, mistakes will always happen in electronics production.” PressFinish is therefore currently pursuing the expansion of its expertise in the area of rework. The two companies are already in contact and the first systems are being tested. The collaboration thus looks set to continue.