As the world leader in the digital transformation of energy management and automation, Schneider Electric, headquartered in Rueil-Malmaison near Paris, puts all its actions at the service of a climate-friendly world. To this end, the company develops intelligent solutions for the optimal use of energy and resources, paving the way for sustainable progress. In Bangalore, India, the company plans to double its production capacity to one million square feet (approximately 93,000 m2) by building a smart factory. No.1 system supplier Ersa has been supporting Schneider Electric´s India business with five wave soldering systems alone since 2019, with more Ersa soldering machines already in the pipeline.
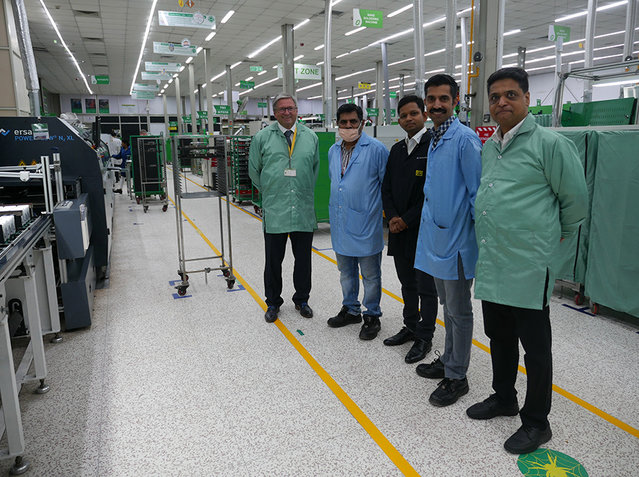
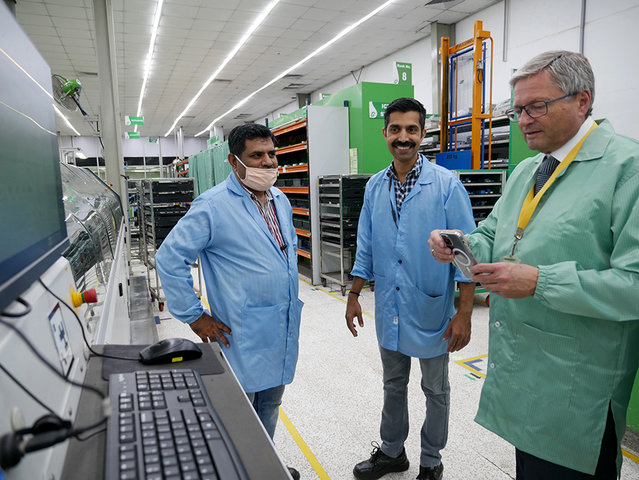
The potential of India´s electronics production is enormous – as evidenced by the bustling Electronic City located in the megacity of Bangalore alone, which is home to numerous electronics and IT industrial parks producing for the Indian market on 800 hectares (3.2 km2). Although manufacturing is increasingly being done for other countries and continents as well. Schneider Electric is also located here with its electronics production – in the Indian market, the global player is targeting sales of 300 million Euro this year, and next year this mark should already be doubled to 600 million Euro. “The important thing is ‘make in India’ – so we are strongly focusing on producing for the Indian subcontinent. But the focus also goes well beyond India´s borders – to North America, for example, where the market is very dynamic and local manufacturing is envisaged,” says Siraj Puthanpurayil, Senior General Manager Manufacturing Technology-Process at Schneider Electric.
Schneider Electric is committed to “Accelerating Sustainability” – with energy-efficient, resource-saving solutions for power supply, among other things, the company wants to enable everyone to participate under the claim “Life is On”. In all growth plans, attention is paid to energy efficiency and a small CO2 footprint; by 2025, Schneider Electric wants to operate in a climate-neutral manner. This applies to its own actions, its own production as well as to the products offered worldwide for areas such as sustainability, software, healthcare and data centers. One concrete example: In 2018, Schneider Electric launched a new product, the “Galaxy VS”, highly efficient scalable UPS with a range of 20 to 150 kW 3-phase UPS for edge, small, and medium data centers and other business-critical applications. “Our UPS is a high-performance product for which there is a large market. However, setting up the production line for this product was anything but easy for our process engineers,” says Siraj Puthanpurayil. With the existing wave soldering machines, there were massive problems in manufacturing – one assembly often took more than 20 minutes, sometimes more than half of an hour, and the quality was not satisfactory. There were discussions with the design team, but it was not possible to re-do the PCB design. There was no way to shake the complex market requirements.
Wave soldering process with 16-kg PCB
Contact was made with Schneider Electric´s European process team and intensive exchanges took place. In addition to two competitors, Ersa GmbH was also included in the benchmarking process. At Productronica 2018, Ersa had presented the POWERFLOW, its new wave soldering system with an individual heating concept, flexible solder bath technology, a new nozzle design and continuous traceability. For the upcoming wave soldering system, a standard machine was already ruled out in advance – because the PCB that was to be produced on it weighed a whopping 16 kg. A real heavyweight among printed circuit boards, large in size and, at 140 to 150 mm components height, also extremely tall. It was not easy to manufacture this component reliably and reproducibly at the highest soldering level. Mr. Christian Ott, the Ersa Area Sales Manager responsible, supported Schneider Electric in the decision-making process and helped to adapt the manufacturing process accordingly. “The decision for our first Ersa POWERFLOW was a real game changer in terms of quality increase and throughput for us! Initially, we were at 10 UPS per day, but with the Ersa machine we now bring it up to 300 pieces per day. This is where our confidence in Ersa machines comes from, that we can manage even the biggest challenges together with the support of the Ersa team,” says Siraj Puthanpurayil. Should a problem nevertheless arise with the PCBs, all parameters are consistently “traceable” and thus clearly can be traced back.
Close support on site in India
“The business partnership with Schneider Electric was one of the decisive reasons for opening our ‘Kurtz Ersa India’ branch here in Bangalore in August 2021. It was clear that we can only provide ‘close support’ here in India with an on-site presence, including spare parts supply – to this end, we now have a well-established team on site, which is being further expanded, and which we supplement via our global remote service Kurtz Ersa CONNECT,” says Ersa General Sales Manager Rainer Krauss. The first machine has since been followed by four more Ersa wave soldering machines from Ersa. Once the business partnership has started, it is growing inexorably – other Schneider subsidiaries in other countries are now also ordering Ersa soldering machines. And of course, Schneider Electric´s mega-production, which will open in a few months, will need more soldering machines to realize the targeted doubling of sales in India – in addition to wave soldering, Schneider Electric´s process technologists are now considering an investment in selective soldering …