From me too to the industry leader in component repair and rework: Since the introduction of the first patented medium-wave infrared rework system in 1997, Ersa has delivered and installed several thousand rework systems and rework stations worldwide. Today, rework systems are used in electronics manufacturing, product development, testing and analysis. Wherever they are used, they maintain the added value of the customer. Ersa now wants to top this even further with the presentation of the latest family members at productronica 2019. With the three hybrid rework systems HR 500, HR 550 XL and HR 600/3P, the company is pushing ahead with the continuous further development of the technology for the benefit of users.
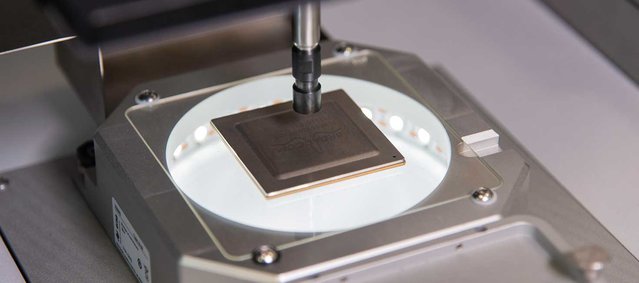
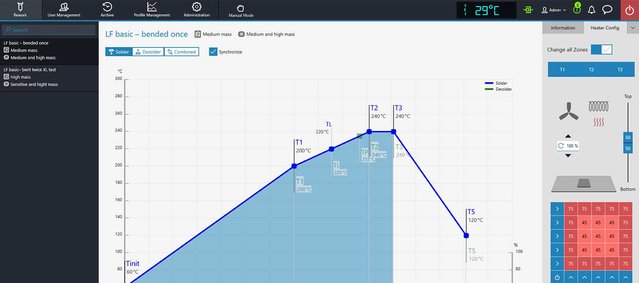
Thanks to the constant new developments of electronics in all fields of industry, new soldering and repair tasks arise almost daily. The drivers for this are progressive miniaturization (chips of size 01005) and new technologies such as 5G with extremely powerful and sometimes very large components (ball grid arrays with 120 x 120 mm edge length). In these very large applications, individually adapted preheating of the assembly is also gaining in importance for preventing distortion of the circuit board. New component shapes and soldered joint designs are being created. It also turns out that the “zero defect” goal is not always achievable in production. Despite the best equipment and highly qualified staff, the many influencing factors mean that defects, which creep in, for example, during new product startups, have to be corrected. The flexibility of the rework systems is an important parameter for being able to cover as wide a range of applications as possible. This applies both to desoldering and soldering processes, which must be carried out as universally as possible and without expensive accessories, and also to component placement. In classic repair, components such as BGA, MLF or QFP are desoldered and replaced with new ones. In service use, faulty assemblies are sometimes put into operation simply by resoldering. Although SMT plugs and sockets as well as special designs are challenging, in general they can also be safely processed.
More developments, more systems
The development departments of many well-known manufacturers use Ersa Rework Systems for prototyping. New housing shapes or components are assembled and soldered for the first time. In even more frequent cases, initial assemblies are provided with newly programmed or modified components. Even the somewhat more exotic fields of analytics or technical forensics often use rework systems. Cross-over tests during troubleshooting are just as common as the desoldering of memory chips from mobile phones or notebooks to analyze the stored data. It is therefore only logical that Ersa should expand its product range and offer its customers appropriate systems to choose from in each case. The ideal application field of the units may well overlap in the process. For example, BGA repair tasks of the same quality can be solved equally well with the HR 600/2 and the HR 550. The current rework range covers practically all SMD components such as are installed in smartphones, notebooks, industrial controllers and high-performance server boards. Customers decide which Ersa system suits them best based on their soldering tasks and requirements.
High performance for soldering and desoldering processes
Ersa hybrid heating technology has been established in the market for several years. The energy input for soldering is a combination of medium-wave infrared radiation and a convection component. Using this technology, assemblies are heated gently and homogeneously. The sensor-guided, closed control loop guarantees precise and repeatable soldering and desoldering processes. External influences are automatically adjusted and largely compensated. The Ersa heating technology does not require any component-specific nozzles and can therefore be used universally. There are no additional costs or waiting times. Damage to surrounding components by hot gases is excluded; miniature components are not blown away. Continuous further development of the technology is reflected in even more efficient heating systems and in the preparation of the connection surfaces. The component connections – for example in the case of BGA, QFP – are automatically immersed in flux or solder paste before soldering. Alternatively, components such as LGA or MLF can also be printed with paste. This results in defined soldered joints which are equal to production quality. In addition to desoldering and soldering processes, the precise placement of multiple-pole components is a fundamental process step. Only minor deviations from the ideal position are permissible. Ersa systems feature automatic placement with image processing or optical systems with excellent image quality for manual alignment. In both cases, the operating software provides practical support for the user while the component is being aligned.
Standardized platform with HRSoft 2
The software package for rework systems has also been further developed and technologically updated. The current HRSoft 2 provides a unified platform for all new rework systems. Easy operation and clear user guidance are just as much a focus as the small amount of familiarization need to use different Ersa units. New features, like a “Minimap” and the “Click in the image”, shorten the time needed to find the working position in very large assemblies. Scaled crosshairs help to grip components exactly in the middle during the desoldering process. In HRSoft 2, all process steps and system states are transparent for the user at all times and are extensively documented. Archiving of the process data makes it possible at any time to verify which parameters have been used to process an assembly. Of course, HRSoft 2 also provides the basis for connecting the units to Manufacturing Execution Systems (MES). Many manufacturers have now seen for themselves that reworking and repair are part of the manufacturing process. As a result, all process data associated with these steps are just as important as line production data. Consequently, it is logical to connect rework systems to the existing MES infrastructure. HRSoft 2 can provide the process parameters required by the customer and establish the link to the relevant order.
Hybrid rework family at its best
The best-selling Ersa IR 550 and the hybrid rework stations HR 100 and HR 200 have already been on the market for many years and have a large fan base. The first automated rework system HR 600/2 and the HR 550 are also already permanent fixtures in the industry. At productonica 2019, Ersa is presenting three brand-new systems for component repair, thus expanding the successful Rework product line. The most recent family members are again characterized by technologically interesting aspects in the field of heating and placement technology and now offer customers an even wider choice.
Advantages of Ersa Rework:
- Successful repair from the first assembly
- No component-specific nozzles required
- homogeneous and material-friendly heating technology
- Stable automatic assembly and soldering processes
- simple operation thanks to user guidance and standardized software
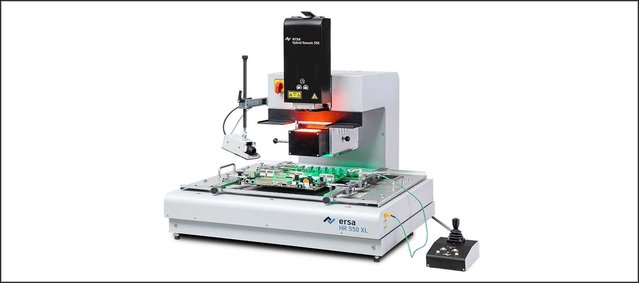
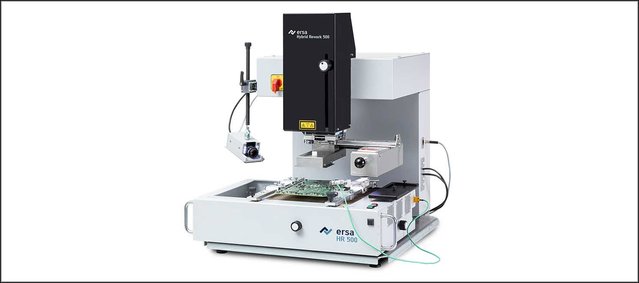
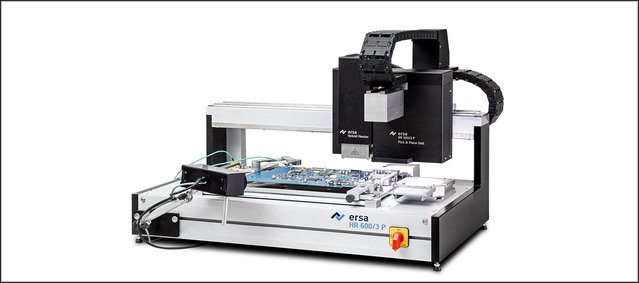