What does Kurtz Ersa CONNECT really have to do with a TV? Technical Report / Digital Services
Digital and smart features, interfaces and platforms offer the industry numerous new opportunities. With the Kurtz Ersa CONNECT platform, system supplier Ersa offers digital added values in process support, system maintenance and employee qualification.
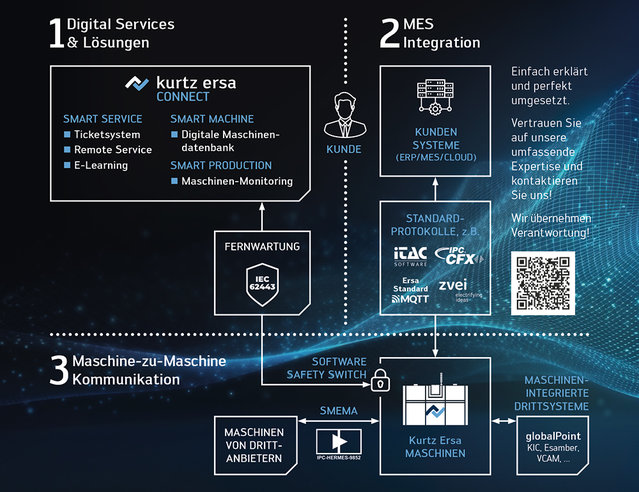
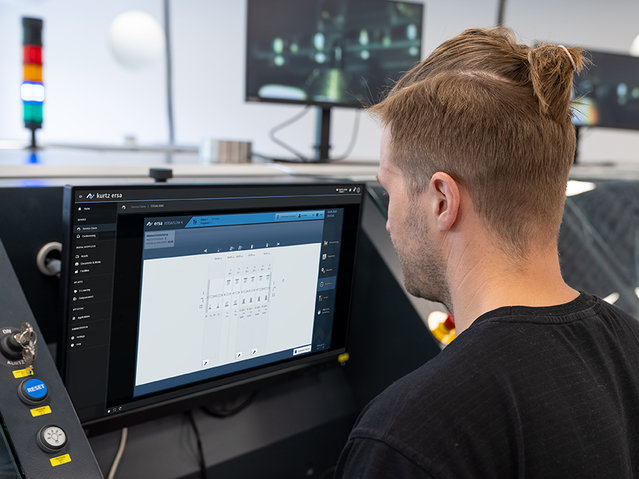
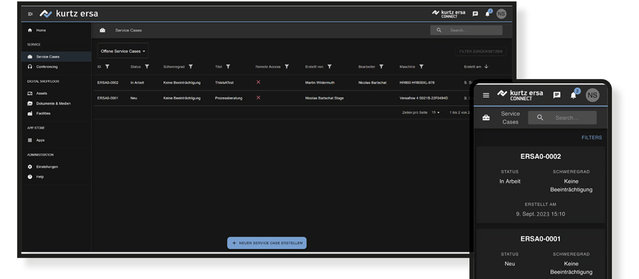
A normal Tuesday. Work routine - after a hard day, it's 8:07 pm on the couch and the daily news program is already running for several minutes. I would have missed the first half in 2014, but today I’m the owner of a Smart TV. „Rewind and start from the beginning “, is my first thought. But things turn out differently: the TV doesn't work and seems to be broken.
For the private individual, the question of what exactly is damaged is of secondary importance. However, the TV manufacturer's view is quite different. There the troubleshooting begins in order to adapt the production process. In the age of digitization, we now use tools such as MES systems for data acquisition and allow the systems on a production line to communicate with each other using the SMEMA standard. We use smart services from machine manufacturers such as ticket systems, remote service or e-learning. Ersa is now consolidating its digitization solutions in the new digital service platform Kurtz Ersa CONNECT to make service processes and process support more cost-effective and even more efficient.
In the area of MES interfaces, Ersa offers standard interfaces such as IPC-CFX. Additionally, there is an Ersa-specific MQTT interface, which provides data via an MQTT broker. This data is in turns collected by a customer MQTT service and forwarded to the customer MES system. The process data stored in a ZVEI file is somewhat simpler. Nevertheless, these also fulfill the purpose of collecting file-based process data. The options for an MES connection are extended by ITAC and customer-specific interfaces.
In a production line, the soldering machine works in series with other machines, including inspection systems, which ensure that the production process meets the quality requirements. Within the line, the machines communicate with each other. This is referred to as “machine to machine communication”. Ersa systems work with the SMEMA and IPC-Hermes-9852 communication standard to communicate data such as the inspection result within the production line. This ensures an efficient production process. Nonetheless, should a problem occur, production can be stopped accordingly, the cause eliminated and the number of rejects substantially reduced.
Ersa enhances these digital functions of its systems with digital services, which are summarized under the term Kurtz Ersa CONNECT. With the Kurtz Ersa CONNECT portal, Ersa offers its customers, the operators of reflow, wave or selective soldering machines, access to these digital services.
Why does a soldering system need this portal?
Let´s look at our example with the Smart TV to answer this question. In this case, data from the MES system helped to improve production and solve quality problems. A smart TV can be found in most households today. You have been able to watch TV on it for decades, but there are additional functions that have led to Smart TVs becoming established thanks to other new features.
The same applies to Ersa soldering systems. The focus here is on the soldering process, but processes around it can still be improved. The Kurtz Ersa CONNECT portal can be accessed via browser or app from any end device and offers access to the various features. One feature is the ticket system, in which customers can enter questions about their machine or process. The Ersa service team then answers these questions in a targeted manner. All information about the process is collected in the ticket and is available to all users. This saves e-mails and phone calls and is ultimately more efficient and, above all, faster for everyone involved.
For more complex issues, an Ersa technician can connect to the machine remotely via the Kurtz Ersa CONNECT portal and check the user interface. The customer alone authorizes access to the machine. Only after the client has enabled it, the remote access from Ersa takes place via an IEC-62443-certified secure connection, which is established via the gateway. The Ersa service employee can gain an insight into the situation and has the option of providing direct support remotely, which ideally saves a service call on site. If this is nevertheless necessary, a detailed overview of the situation is already available thanks to the prior remote access and the deployment can be optimally prepared.
Another feature of Kurtz Ersa CONNECT is the system management from the customer's point of view, so that a machine park that is distributed across different plants can be displayed accordingly. Tickets are thus easy to retrieve and can be filtered for specific machines. At the same time, documents such as maintenance schedules, drawings, plans and the like can be stored at machine level, making access as easy as possible for the operator.
E-learning - generating the same level of knowledge despite fluctuation and skills shortages
Ersa offers an extensive e-learning program to give machine operators and interested parties a more comprehensive understanding of the soldering process and the soldering system. Interactive courses are used to clearly explain the details of the machine and the soldering process. The mix of video, sound, images and text in combination with knowledge tests makes the courses lively and appealing. Interim tests make learning progress measurable and transparent. The e-learning module complements the range of seminars and training courses on site in Wertheim. Just like the ticket system, e-learning is a feature that can be used offline anywhere in the world without a direct connection to the machine.
The situation is different for functions that rely on data from the machine, such as remote service, but also any display of data from the machine. In this case, the data is made available via the built-in gateway of the Kurtz Ersa CONNECT platform. In order to be able to access the status of the machine and its efficiency anywhere in the world via the Kurtz Ersa CONNECT platform, Ersa is working on a dashboard that displays and provides this information about the machine.
To make the television of tomorrow as pleasant as possible for the customer, there will be new and additional smart features in the future. What applies to television can be transferred to Ersa and the soldering process. With KE-CONNECT, all the prerequisites have been created to be able to offer even more smart features in the future and to further increase customer benefits.
Advantages Kurtz Ersa CONNECT
- Improvement of the service process through the ticket system incl. remote service
- Knowledge transfer and development via eLearning
- Process optimization via display of the machine status (in implementation)