EPP Pre-Expander Pre-Expander
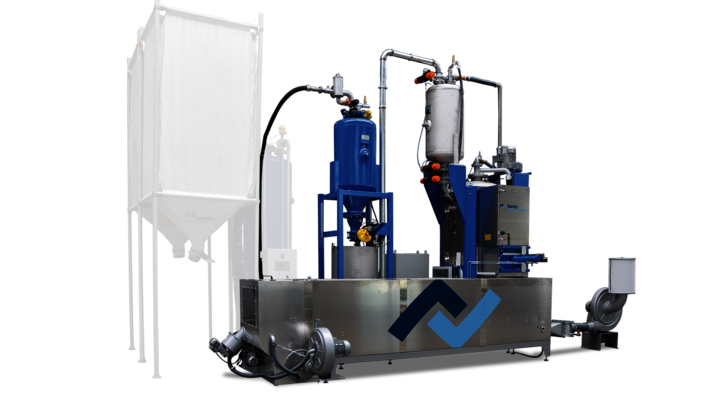
Reduction of material use and conservation of resources
Advantages Kurtz EPP Pre-ExpandersEPP Pre-Expander
-
Uniform bulk density distribution
-
Homogeneous temperature distribution in the pre-expansion vessel
-
Stabilization of EPS beads in the fluidized bed
-
High material throughput
-
Low energy consumption
EPP Pre-Expander
Highest Efficiency
With the use of a Kurtz EPP pre-expander, a truck can transport up to five times the raw material weight per trip, resulting in enormous cost savings. The potential savings in raw material consumption that can thus be achieved make it possible to amortize the cost of the investment within 2 years at a throughput of approximately 100 t per month.
Pre-foaming process: first step to success
The EPS raw material is conveyed as granules to the preexpander, where it is heated by means of wet steam. The hot steam softens the polystyrene beads and activates the blowing agent dissolved in them. This evaporates and causes the softened beads to expand. The bulk density can be adjusted by the weight of the raw material and the foamed volume. The EPS beads pre-expanded in this way are then cooled and stabilized in a fluidized bed on an air cushion before being conveyed by blower via a rotary feeder into the silos.
Welding of the end products
During the subsequent intermediate storage, the blowing gas diffuses out of the pre-expanded polystyrene beads and air penetrates. This "packed air" is further processed in the converting process on an automatic moulding machine or in a block mould. To achieve low bulk densities, EPS can also be post-foamed in a second pass. For expandable polypropylene (EPP), EPP/HP pre-expanders are available for lightweight foaming.
Technical DataEPP Pre-Expander
Prozess Optimization
-
Bulk density control
-
Rotary feeder for material discharge into silo
-
Weighing device for starting material
-
Cover slotted screen for homogeneous temperature distribution
-
Exact pressure control +/- 0.1 bar
Options
-
Overfill protection for fluidized bed
-
Data storage
-
Automatic silo control
-
Weighing device for starting material
-
Exact pressure control +/- 0.1 bar
Accessories
-
Suction conveyor
-
Pressure loading tanks
-
Heating register
-
Cleaning function
Related ProductsEPP Pre-Exander
Find a contact
Find a contact
Haben Sie Fragen zu unseren Produkten und Services? Kontaktieren Sie uns, wir sind für Sie da!