EPS Pre-Expander Pre-Expander
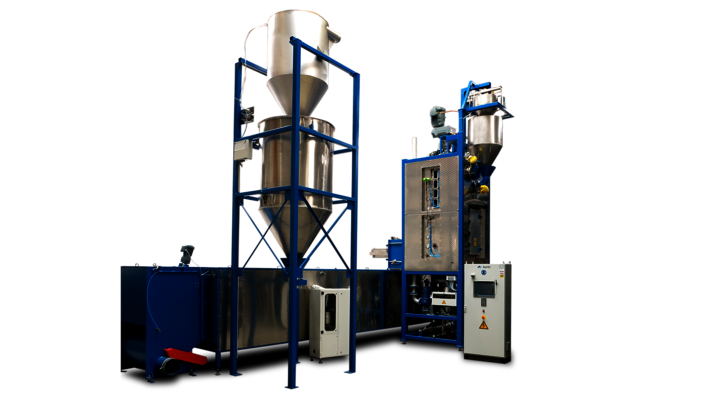
Economic advantages all along the line
Advantages of Kurtz EPS Pre-ExpandersEPS Pre-Expander
-
Even density distribution
-
Homogeneous temperature distribution in the pre-expanding boiler
-
Stabilization of EPS-beads in the fluid bed
-
High material throughput
-
Low energy consumption
Pre-foaming process: first step to successEPS Pre-Expander
The EPS raw material is conveyed as granules to the pre-expander, where it is heated by means of wet steam. The hot steam softens the polystyrene beads and activates the blowing agent dissolved in them. This evaporates and causes the softened beads to expand. The bulk density can be adjusted by the weight of the raw material and the foamed volume. The EPS beads pre-expanded are then cooled and stabilized in a fluidized bed on an air cushion before being conveyed by blower via a rotary feeder into the silos.
Welding of the end products
During the subsequent intermediate storage, the blowing gas diffuses out of the pre-expanded polystyrene beads and air penetrates. This "packed air" is further processed on an automatic molding machine. To achieve low bulk densities, EPS can also be post-foamed in a second pass.
For expandable polypropylene (EPP), EPP/HP pre-expanders are available for lightweight foaming. This can significantly reduce logistics costs.
Technical DataEPS Pre-Expander
Prozess Optimisation
-
Density control
-
Electrical temperature control for high densities
-
Cellular wheel sluice for material transport to the silo
Options
-
After foaming facility for low densities
-
Overfill safety for fluid bed
-
Wedge wire sieve for big pre-expanders
-
Data memory
-
Automatic silo control
Applications
-
All EPS raw material
-
Copolymers with EPS percentage
Related ProductsEPS Pre-Expander
Find a contact
Find a contact
Haben Sie Fragen zu unseren Produkten und Services? Kontaktieren Sie uns, wir sind für Sie da!