Allmendinger Elektromechanik relies on professional component repair
For nearly 30 years, Allmendinger Elektromechanik KG has been serving customers around the world with repairs, spare parts, service on site and a retrofit program for CNC machines. The company with a workforce of 200 specializes in the supply and repair of Siemens CNC controls, PLC controls, servo and spindle drives as well as servo motors. Whether for current models or for obsolete systems that have already been discontinued by industrial giant Siemens - Allmendinger provides first-class support for companies such as Indramat, Heidenhain, Fanuc, Bosch, Kuka and many more. Two Ersa HR 550 rework systems play a key role in maintaining added value. This saves costs and is sustainable.
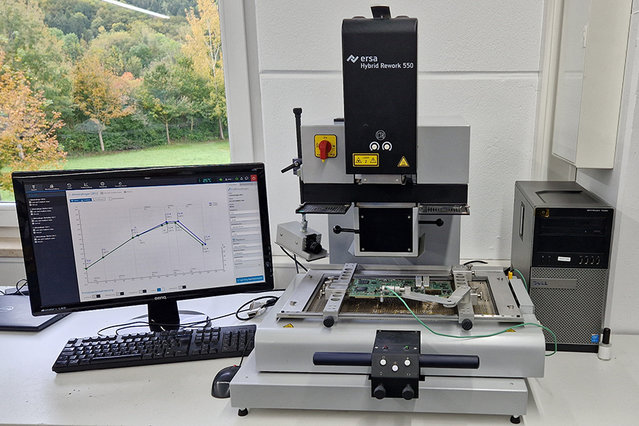
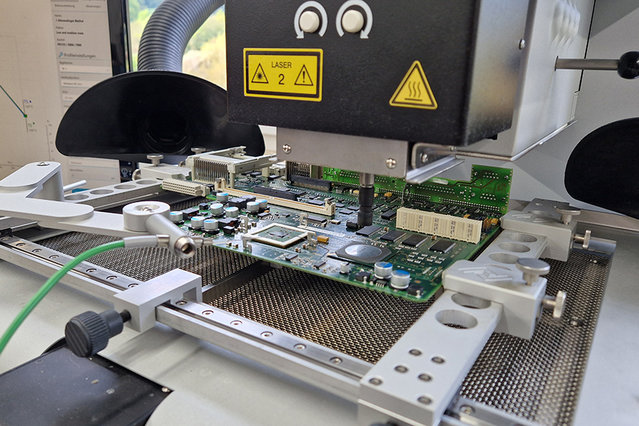
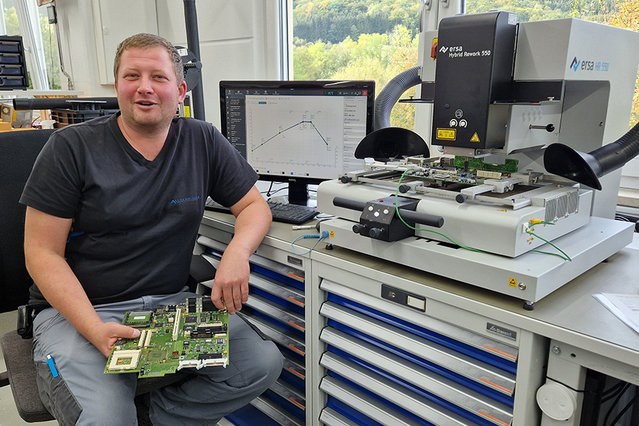
What does a classic service case look like for the Swabian family-owned company, which was founded in 1996 by Senior Director Hermann Allmendinger as a one-man operation with a great deal of pioneering spirit and has been growing continuously ever since? “As a rule, our customers only contact us when there is already an acute defect,” say Nadine and Daniel Allmendinger, Managing Directors in the second generation, describing the regularly recurring process. “Then it has to be done quickly. This is where our core competencies come into play - cross-manufacturer repairs of all electronic assemblies at a fixed price for Siemens, Indramat, Heidenhain, Fanuc and Bosch. If required, we can offer direct exchange and express delivery. Our primary goal is to minimize the downtime of high-end production systems - to achieve this, we use the latest measuring and production technology, such as around 110 test benches developed in-house or our own X-ray system.” This is based on Allmendinger´s motto: “Everything. Fast. Fair.” It is also reflected in the certifications the company has acquired over time: These include DIN EN ISO 9001 (since 2011), which specifies requirements for quality management systems and is based, for example, on customer expectations, and DIN EN ISO 14001 (since 2014), which certifies that the company operates in accordance with valid environmental guidelines.
Back to the service case: Error analysis and data backup are carried out at the highest technical level, for example for the Siemens Sinumerik series, Simatic panels and Heidenhain CNC controls. A 24/7 webshop with direct access to more than 40,000 different spare parts in a storage area of around 50,000 m² is an elementary component of the company´s service. Ersa HR 550 rework systems and soldering tools play a central role in the repair of electronic assemblies at board level. The range of repair services is as diverse as their causes. Customer-specific components are often no longer available, so they must be “rescued” and reused. Equally essential is the reuse of components for older control units for which replacements are no longer directly available.
Customer base comprising small businesses to automotive corporations
The Swabian company´s customer base ranges from small businesses to major automotive corporations. Two rework systems for repairing electronic assemblies are an integral part of the success story. According to electronics technician Julian Feder, who has been responsible for assembly repair in the workshop since 2013, the HR 550 hybrid rework systems are used individually on many different assemblies. “Older assemblies, sometimes up to 40 years old, are often brought back to working order with the help of the Ersa systems.” As a result, about 60 to 70 percent of rework applications contain leaded solders. These boards are processed by selecting profiles stored in the databank of the HRSoft 2 operating software. When there are no special or high-priority jobs, the rework systems run all day, and between five and ten assemblies are reworked or repaired each day.
BGA Reballing
The biggest share of new electronic components (BGAs) is sourced from China. If components for single assemblies are not available, existing BGAs (e.g. Intel chips or graphics chips) will obtain new solder balls in a so-called reballing process. According to Julian Feder, one can expect a success rate of 80 percent when reballing. Removing glue dots is a further challenge prior to exchanging BGAs on some control unit assemblies. Another challenge is the removal of adhesive dots prior to BGA replacement on some control unit assemblies. Since December 2016, the company has been relying on the HR 550 rework system, which provides excellent results thanks to its simple and convenient operation with guided processes, a high-performance optical system and flexible heating technology. The system has been upgraded with the latest hardware and software over the years. Two such systems are operating at Allmendinger today, and it is quite possible that more soldering systems from Ersa in Wertheim will find their way to the CNC specialists in future ...
Categories
Author of the Article
Ralf Walk
Area Sales Manager
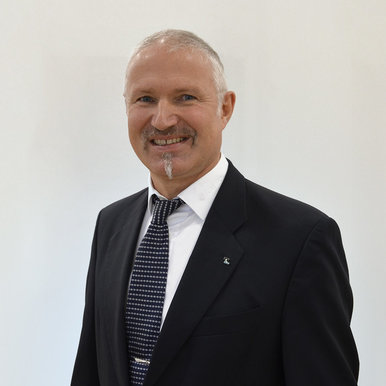