VERSAPRINT 2 TIM Ersa Stencil Printing

Economical and reproducible thermal paste printing
For the efficient use of power semiconductors such as IGBTs, the optimum electrical connection to the PCB and a high-quality thermal connection to the heat sink (housing or heat sink) must be created. The ideal combination for a high-quality assembly process is the VERSAFIT 500 press-fit system for the electrical connection and the VERSAPRINT 2 TIM (Thermal Interface Material) stencil printer for the thermal connection for heat dissipation.
VERSAPRINT 2 TIMTechnical highlights
- Component clearance below up to 100 mm
- Alignment accuracy +/- 12.5 µm @6s
- Squeegee force control with closed loop
- Paste roll diameter detection
- Paste feeding from large containers
- Heavy-duty transport up to 15 kg
- Integrated 3D inspection
- Flat belt transport
- Options can be retrofitted in the field
VERSAPRINT 2 TIMErsa Videos
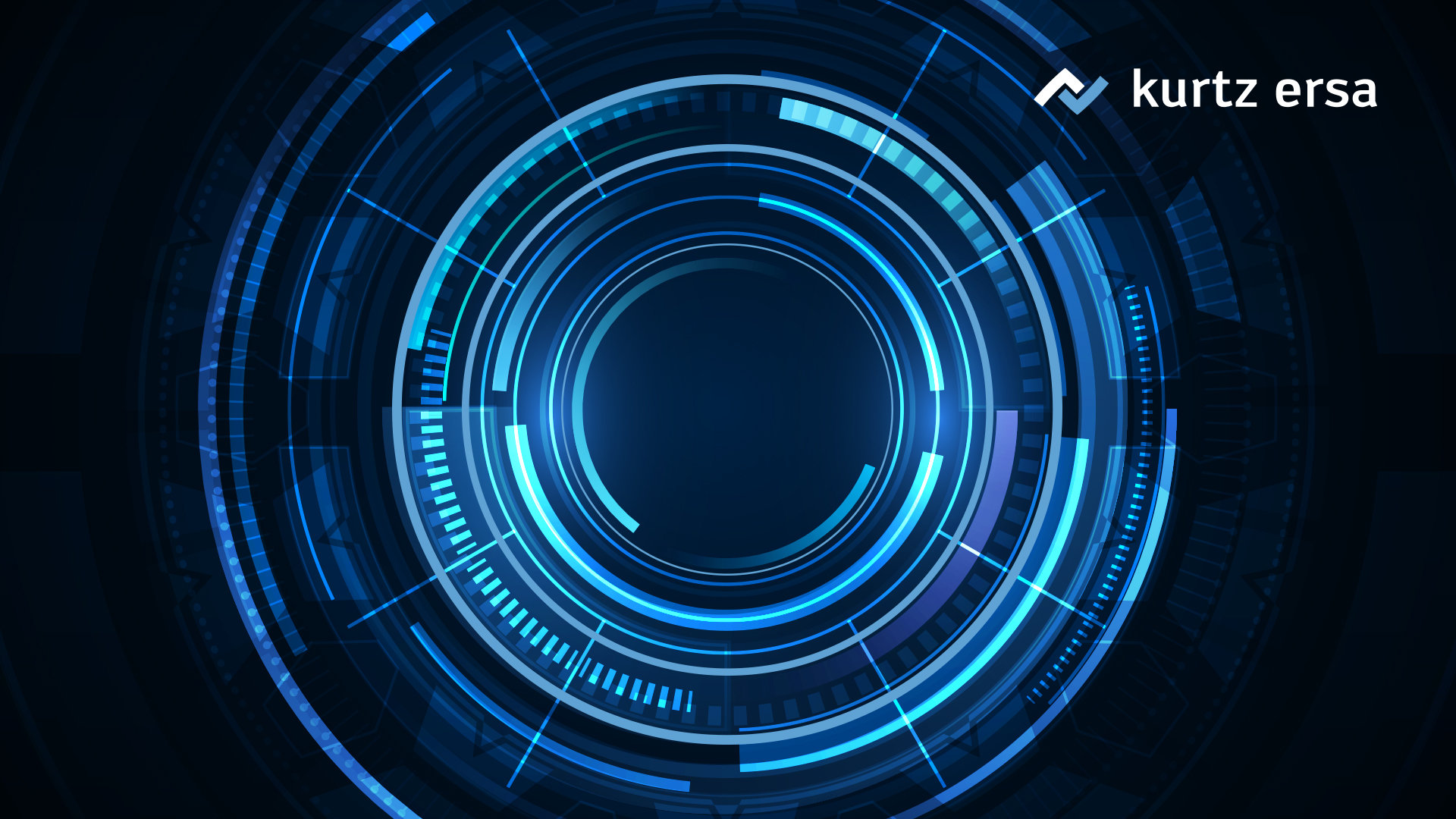
Ersa Stencil Printer – VERSAPRINT 2 Ultra³ – product video
Direct coupling of press-fit and printing processErsa VERSAPRINT 2 TIM
After the press-fit process, the assembly is automatically transported to the printer, where thermal paste is printed onto the IGBTs. The direct coupling of the press-fit and printing process saves handling steps and increases the throughput of the line. The VERSAPRINT 2 TIM offers all the advantages of stencil printing combined with precise process parameters for optimum processing of thermal pastes. This achieves reproducible volume application, which can also be monitored using the printer's integrated inspection system. Together, VERSAFIT 500 and VERSAPRINT 2 TIM form a high-performance team for power electronics applications.
Ersa Success StoriesVERSAPRINT 2 TIM
VERSAPRINT 2 TIMErsa Stencil Printing
Technical data
- Component clearance below up to 100 mm
- Alignment accuracy +/- 12.5 µm @6s
- Squeegee force control with closed loop
- Paste roll diameter detection
- Paste feeding from large containers
- Heavy-duty transport up to 15 kg
- Integrated 3D inspection
- Flat belt transport
- Options can be retrofitted in the field
Basic configuration
- Program-controlled width adjustment
- Automatic mark recognition
- Automatic stencil underside cleaning
- Efficient program creation
- Touch operation
- High ease of maintenance